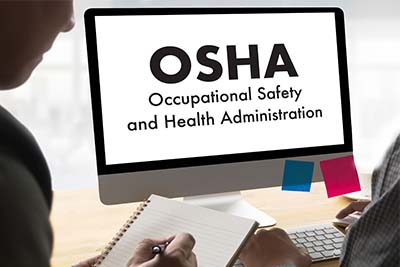
OSHA and the Automotive Industry
OSHA stands for Occupational Safety and Health Administration. It is a United States federal agency that operates under the Department of Labor. OSHA's primary goal is to ensure safe and healthy working conditions for employees by setting and enforcing workplace safety and health regulations.
OSHA was established in 1970 with the passage of the Occupational Safety and Health Act, which authorized OSHA to develop and enforce workplace safety and health standards, as well as provide training, outreach, education, and assistance to employers and workers.
OSHA has jurisdiction over most private sector employers and their employees, as well as some public sector employers and employees in the 50 states and certain territories and jurisdictions under federal authority. OSHA is responsible for inspecting workplaces, investigating complaints of workplace hazards, and issuing citations and penalties for violations of OSHA standards.
OSHA posters for your business in many different languages are available online - OSHA's Free Workplace Poster | Occupational Safety and Health Administration
When does OSHA Inspect a Business?
OSHA (Occupational Safety and Health Administration) may inspect a business for a variety of reasons, including in response to a complaint or referral, a severe accident or incident, a programmed inspection, or as part of a follow-up inspection to ensure that previously identified hazards have been corrected.
Here are some specific scenarios that may trigger an OSHA inspection:
- Complaint or referral: An employee or a member of the public can file a complaint or referral with OSHA, which may prompt an inspection if the complaint is credible and falls within OSHA's jurisdiction.
- Severe accident or incident: OSHA may investigate a workplace accident or incident that results in a fatality, hospitalization of three or more employees, or the potential release of a hazardous substance.
- Programmed inspection: OSHA conducts programmed inspections on high-hazard industries or workplaces with a history of serious safety and health violations.
- Follow-up inspection: OSHA may conduct a follow-up inspection to ensure that previously identified hazards have been corrected and the workplace is now in compliance with OSHA regulations.
It's important to note that OSHA inspections are typically unannounced, meaning that employers should always strive to maintain a safe and healthy workplace to avoid potential fines, penalties, and reputational damage associated with safety violations.
What are common OSHA Violations in the automotive Industry?
There are several OSHA violations that are common in the automotive industry. Some of the most frequent violations include:
- Failure to provide adequate respiratory protection: Automotive workers are often exposed to hazardous substances such as paints, solvents, and other chemicals that can cause respiratory problems. Failure to provide proper respiratory protection can lead to serious health issues.
- Failure to provide adequate eye protection: Automotive workers are also often exposed to flying debris, sparks, and other hazards that can cause eye injuries. Failure to provide proper eye protection can lead to serious eye injuries and blindness.
- Failure to provide proper machine guarding: Automotive workers operate heavy machinery and equipment, which can cause serious injuries if they are not properly guarded. Failure to provide adequate machine guarding is a common OSHA violation in the industry.
- Failure to provide proper training: Automotive workers need to be properly trained in the safe operation of equipment, handling hazardous materials, and other safety procedures. Failure to provide adequate training is a violation of OSHA regulations.
- Failure to provide proper fall protection: Automotive workers often work at heights, such as when working on vehicles on lifts or working on roofs. Failure to provide proper fall protection, such as guardrails or personal fall arrest systems, is a common OSHA violation in the industry.
- Failure to properly label hazardous chemicals: Automotive workers work with a variety of hazardous chemicals, and failure to properly label these chemicals can lead to serious health consequences.
- Failure to properly store hazardous chemicals: Automotive workers also need to properly store hazardous chemicals to prevent fires and other accidents. Failure to store hazardous chemicals properly is a violation of OSHA regulations.
It is important for employers in the automotive industry to be aware of these common OSHA violations and take steps to address them to ensure the safety of their workers.
What should you do if your business receives an OSHA Violation?
If your business receives an OSHA violation, there are several steps you should take to address the violation and ensure compliance with OSHA standards.
- Review the Citation: Carefully review the citation and any supporting documentation provided by OSHA to understand the nature of the violation and the specific OSHA standard(s) that were cited.
- Correct the Violation: Correct the violation promptly and take steps to ensure that it does not recur. Keep detailed records of the corrective actions taken.
- Contest the Citation: If you believe that the citation was issued in error or that the penalty is unwarranted, you have the right to contest the citation. The citation will provide instructions on how to contest the citation, including the deadline for filing a notice of contest.
- Communicate with OSHA: If you need additional time to correct the violation or have questions about the citation, communicate with the OSHA area director or compliance officer who issued the citation.
- Train Employees: Ensure that employees are trained on the hazards identified in the citation and on any new policies or procedures implemented to prevent future violations.
- Keep Records: Keep records of all communications with OSHA, corrective actions taken, and employee training to demonstrate your commitment to safety and compliance.
It is important to take OSHA violations seriously and address them promptly to ensure the safety and health of your employees and avoid further penalties or legal action.
How to Avoid OSHA Violations?
To avoid OSHA violations, your business should take a proactive approach to workplace safety and health. Here are some steps you can take to minimize the risk of OSHA violations:
- Know the Standards: Familiarize yourself with the OSHA standards that apply to your industry and ensure that your workplace is in compliance.
- Conduct a Hazard Assessment: Conduct a comprehensive hazard assessment of your workplace to identify and address potential hazards.
- Implement Safety Programs: Implement safety programs, policies, and procedures to address identified hazards and prevent workplace injuries and illnesses.
- Train Employees: Ensure that employees are trained on workplace hazards and safe work practices, including any new or updated policies or procedures.
- Provide Personal Protective Equipment (PPE): Provide appropriate personal protective equipment (PPE) to employees and ensure that it is used and maintained correctly.
- Maintain Records: Maintain accurate records of workplace injuries and illnesses, safety training, and safety inspections to demonstrate compliance with OSHA standards.
- Participate in OSHA Consultation Programs: Participate in OSHA consultation programs, which provide free and confidential advice on improving workplace safety and health.
- Respond to Employee Complaints: Promptly respond to employee complaints regarding workplace hazards and take appropriate corrective action.
By taking these steps, your business can create a culture of safety and health that prioritizes the well-being of employees and minimizes the risk of OSHA violations.
Arrowhead Automotive Insurance can assist you with ways to try to avoid an OSHA violation
The experienced Account Executives at Arrowhead Automotive Insurance can play a valuable role in helping a business avoid OSHA violations by providing risk management advice and resources.
Here are some ways an insurance agent can help:
- Conduct a Risk Assessment: An insurance agent can help a business conduct a risk assessment to identify potential workplace hazards and develop strategies for mitigating them.
- Review Safety Programs: An insurance agent can review a business's safety programs, policies, and procedures to ensure that they are in compliance with OSHA standards and best practices.
- Provide Safety Resources: An insurance agent can provide resources, such as safety training materials and templates for safety policies and procedures, to help a business maintain a safe and healthy workplace.
- Offer Safety Training: An insurance agent can offer safety training to employees and management to ensure that everyone is aware of potential hazards and knows how to prevent workplace injuries and illnesses.
- Assist with Compliance: An insurance agent can assist a business in complying with OSHA regulations, including record-keeping and reporting requirements.
- Provide OSHA Insights: An insurance agent who is knowledgeable about OSHA regulations can offer insights and advice on compliance issues and best practices.
- Recommend Safety Products: An insurance agent can recommend safety products, such as personal protective equipment and safety equipment, to help a business maintain a safe and healthy workplace.
By working with the experienced insurance professionals at Arrowhead Automotive Insurance, a business can benefit from their expertise in risk management and safety and take a proactive approach to avoiding OSHA violations.